DDGS-Milling System
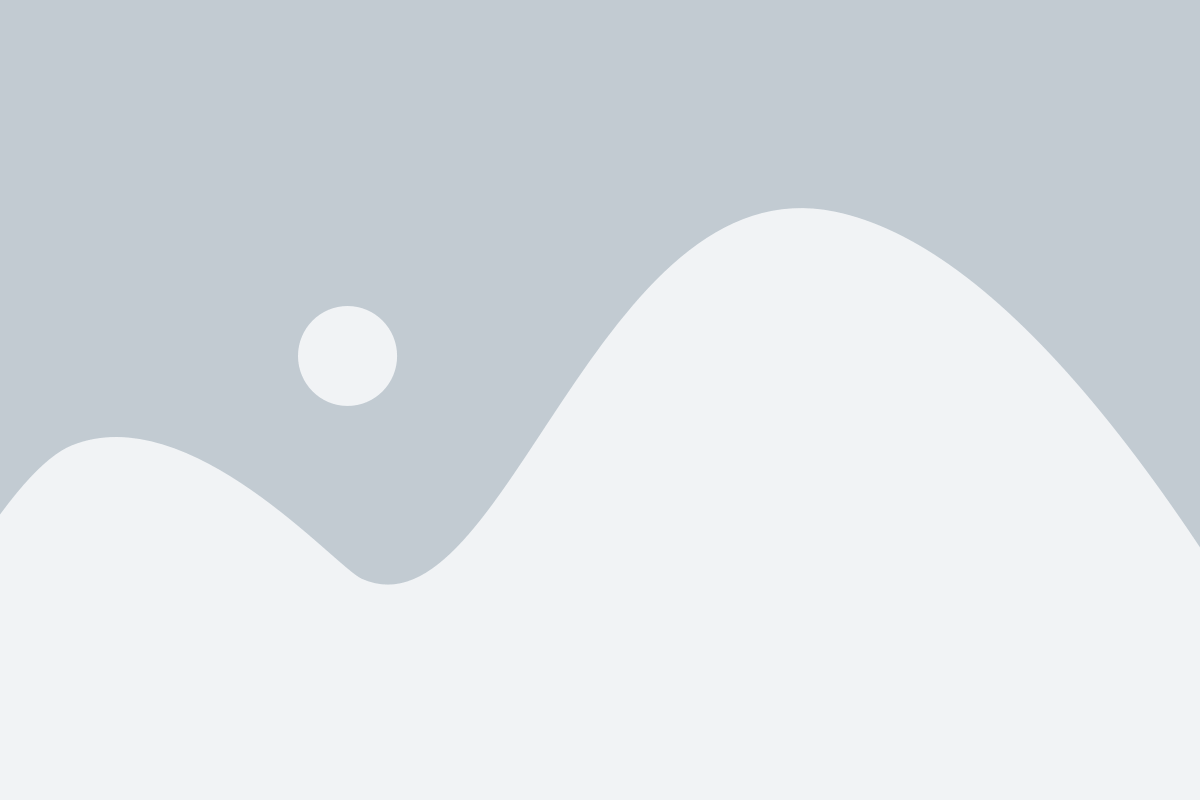
DDGS-Milling System
Introduction
The Distillers Dried Grains with Solubles (DDGS) milling system is an essential part of the ethanol production process. It involves the grinding of dried grains to produce a fine, uniform product that is widely used as high-quality animal feed. Proper milling ensures that the final product meets industry standards and enhances the value of DDGS as a marketable commodity. At AESS Pune, we specialize in designing and installing advanced DDGS milling systems that offer excellent performance, durability, and energy efficiency. In this article, we’ll explore the importance of a well-functioning DDGS milling system, the key steps involved, and the benefits of using a high-quality system.
DDGS Milling System: A Complete Overview for Maximum Efficiency at AESS Pune
Why Is a DDGS Milling System Important?
DDGS is a byproduct of ethanol production, rich in proteins, fibers, and fats, making it an excellent feed supplement for livestock. However, to optimize its use in the feed industry, it must be ground into a uniform size and texture. A reliable DDGS milling system helps in producing fine, consistent granules, which improves feed digestibility for animals. Efficient milling not only ensures product quality but also maximizes production output and reduces wastage, making it a critical component in ethanol production facilities.
Signs You Need a DDGS Milling System Upgrade
To maintain high production efficiency, it’s important to ensure that your DDGS milling system is in top condition. Here are some signs that you may need to consider upgrading or replacing your current system:
- Inconsistent Particle Size: If your DDGS output varies in size, it could negatively affect its quality and marketability.
- Reduced Milling Speed: A decline in milling speed leads to lower production output, which can affect the overall profitability of your operation.
- High Energy Consumption: Outdated systems often require more energy to achieve the same results, leading to increased operational costs.
- Frequent Downtime: If your milling system requires frequent repairs or breaks down often, it may be time to invest in a more efficient and reliable solution.
DDGS Milling System Process at AESS Pune
At AESS Pune, we follow a comprehensive process to ensure that our DDGS milling systems provide optimal performance and durability. Here’s how we manage the installation and maintenance of a DDGS milling system:
1. Initial Assessment and System Design Before designing the milling system, AESS Pune’s experts conduct a detailed assessment of your facility’s requirements. We take into account factors such as production capacity, desired particle size, and energy efficiency. This allows us to design a custom DDGS milling system tailored to your specific needs, ensuring that it operates with maximum efficiency.
2. Selection of Milling Equipment Choosing the right milling equipment is crucial for the system’s performance. At AESS Pune, we offer a variety of milling solutions, including hammer mills and roller mills, depending on your production requirements. Our equipment is designed for durability and precision, ensuring consistent particle size and minimizing dust generation during the milling process.
3. Installation and Integration Once the equipment is selected, our team handles the installation process with precision. We ensure seamless integration of the milling system with your existing production line, optimizing airflow and minimizing downtime during the installation. Proper alignment and setup of the milling machinery are critical to ensure that it operates at peak performance from the start.
4. Fine-Tuning for Optimal Performance After installation, AESS Pune’s technicians fine-tune the milling system to meet your specific production goals. This involves adjusting settings for particle size control, ensuring that the output is consistent and meets industry standards. We also optimize energy usage to reduce operational costs while maximizing output efficiency.
5. Testing and Quality Assurance Once the system is set up, it undergoes rigorous testing to ensure that it functions as intended. We measure particle size uniformity, milling speed, and energy consumption to ensure that all performance metrics are met. At AESS Pune, we prioritize quality assurance to guarantee that our milling systems deliver reliable, long-term results.
6. Ongoing Maintenance and Support A well-maintained DDGS milling system is essential for uninterrupted production. At AESS Pune, we offer regular maintenance services to keep your system running smoothly. Our support includes routine inspections, wear and tear checks, and timely replacement of worn-out components to prevent unexpected breakdowns.
Key Benefits of Using a High-Quality DDGS Milling System
Investing in an advanced DDGS milling system from AESS Pune offers several benefits, including:
- Enhanced Product Quality: A consistent particle size improves the overall quality of DDGS, making it more marketable and easier for livestock to digest.
- Increased Production Efficiency: Modern milling systems are designed to handle higher volumes at faster speeds, allowing you to increase your production capacity without sacrificing quality.
- Reduced Operational Costs: Efficient systems use less energy and require fewer repairs, leading to long-term savings on operational expenses.
- Lower Dust Levels: Properly designed systems reduce the amount of dust generated during the milling process, improving workplace safety and air quality.
- Durability and Reliability: AESS Pune’s milling systems are built to withstand the wear and tear of continuous operation, ensuring long-lasting performance and reduced downtime.
Materials Used in DDGS Milling Systems
At AESS Pune, we use durable, high-quality materials to ensure the longevity and efficiency of our milling systems. These materials are carefully selected to meet the unique requirements of DDGS milling:
- Stainless Steel: Resistant to corrosion, stainless steel is ideal for systems that require high durability and minimal maintenance.
- Hardened Steel: Used for wear-resistant components, hardened steel extends the life of critical parts, reducing the need for frequent replacements.
- Composite Materials: For specific components, we use advanced composites to improve wear resistance and reduce system weight, enhancing overall performance.
When to Consider Upgrading Your DDGS Milling System
Several factors can indicate that it’s time to upgrade your DDGS milling system:
- Increased Production Needs: If your facility is expanding or you’re processing more DDGS than your current system can handle, an upgrade is necessary to maintain efficiency.
- Frequent Repairs: If your system requires frequent repairs and maintenance, upgrading to a more modern, reliable solution will save you money in the long run.
- Energy Inefficiency: Rising energy costs and poor system efficiency can make an older milling system more expensive to operate.
- Inconsistent Product Quality: If your current system isn’t producing a uniform particle size, an upgrade can improve product quality and marketability.
Conclusion
A reliable and efficient DDGS milling system is vital for ethanol production facilities looking to maximize output and improve product quality. At AESS Pune, we provide top-of-the-line DDGS milling systems that are designed to meet the specific needs of your facility, ensuring consistent particle size, energy efficiency, and durability. Whether you need a new system installation, an upgrade, or ongoing maintenance, AESS Pune has the expertise and solutions to help you optimize your DDGS milling process. Contact us today to learn more about how we can support your milling system needs and keep your